Since photovoltaic power generation began to be applied on a large scale in power plants, manufacturers have sought to reduce production costs and scale up manufacturing. This has led to the development of increasingly larger solar cells, from the early 125mm × 125mm sizes to over 210mm × 210mm. Consequently, the power of basic photovoltaic modules has increased from 100W+ to over 700W+.
However, with this increase in power, module weight has also risen significantly, reaching approximately 35kg per module or 12.4kg/m². Including mounting brackets, the weight increases to around 16kg/m². Such heavy modules pose challenges for installation on large-span industrial and commercial rooftops, which often have limited load-bearing capacity. This limitation prevents the installation of traditional modules on such roofs, creating a bottleneck in the industry's development.
Challenges and Innovations
To address this, reducing the weight of module packaging has become a key focus. Flexible modules that can adapt to the contours of various architectural surfaces are in high demand. Initial attempts involved thinning the glass and optimizing aluminum alloy frames. For example, reducing glass thickness from 3.2mm to 2.0mm decreased weight by about 3kg/m². However, thinner glass compromises module strength, necessitating smaller module sizes to meet reliability standards, thus failing to resolve the core issue.
Large-scale modules with glass packaging are still cumbersome for rooftop installation and prone to breakage during transportation and construction, posing safety risks. As a result, glass-encased modules are better suited for ground-mounted power plants.
The search for alternative materials to replace glass in module packaging has been ongoing. Lightweight encapsulation materials with enhanced performance have made non-glass packaging a viable solution.
Advances in Lightweight Materials
Early lightweight modules used fluoropolymer films and fiberglass backplates for support, replacing glass. While suitable for waterproof and flexible roofs (e.g., TPU-coated surfaces with adhesive mounting), the backplates were still too thick, leaving module weight around 8kg/m².
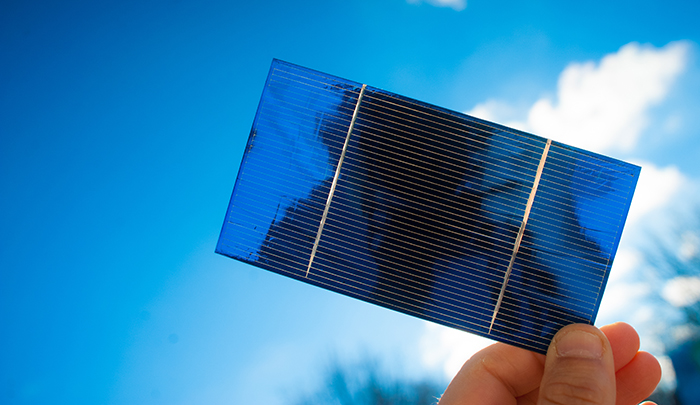
In recent years, advancements in composite materials and modified polymers have achieved encapsulation performance comparable to glass. These materials enable lightweight modules to meet industry standards for a 25-year operational lifespan, providing photovoltaic performance equivalent to glass modules. This breakthrough has accelerated the adoption of non-glass packaging solutions, particularly for rooftop applications, expanding the scope of photovoltaic installations.