In addition to the main equipment, such as photovoltaic modules, inverters, and step-up transformers supporting the connection of photovoltaic cable materials on the photovoltaic power plant of the overall profitability of the ability to run the safety, whether efficient, also plays an important role.
In recent years, the application of solar energy (PV) power generation is becoming more and more widespread, rapid development, in the construction process of photovoltaic power plants, in addition to the main equipment, such as photovoltaic modules, inverters, step-up transformers, in addition to supporting the connection of photovoltaic cable materials on the photovoltaic power plant's overall profitability, operational safety, whether high efficiency, also plays a crucial role. The following is a full overview of the common cables and materials used in PV power plants, as well as their environmental impact.
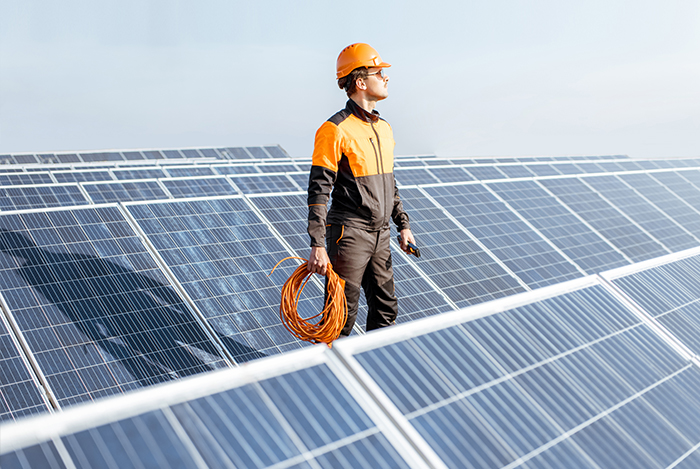
In recent years, the application of solar energy (PV) power generation is becoming more and more widespread, rapid development, in the construction process of photovoltaic power plants, in addition to the main equipment, such as photovoltaic modules, inverters, step-up transformers, in addition to supporting the connection of photovoltaic cable materials on the photovoltaic power plant's overall profitability, operational safety, whether high efficiency, also plays a crucial role. The following is a full overview of the common cables and materials used in PV power plants, as well as their environmental impact.
According to the system of PV power plants, cables can be classified into DC cables and AC cables, and are classed as follows based on the varied purposes and environments of use:
1. DC Cable
(1). Series cables connect modules to modules.
(2). Between the strings and their strings and the DC distribution box (convergence box) via the parallel connection.
(3). Connect a cable between the DC distribution box and the inverter.
The cables listed above are DC cables, which must be moisture-proof, resistant to sun exposure, cold, heat, and UV radiation. In some cases, acid, alkali, and other chemical substances must also be avoided.
2. AC Cable
(1). Connect the inverter to the step-up transformer using the cable.
(2). The cable connecting the step-up transformer to the electricity distribution unit.
(3). Distribution unit for the grid or the user's connection cable.
This section of the cable is for the AC load cable, which is laid in an indoor environment in accordance with the general power cable selection standards.
3. Photovoltaic special cable
A high number of DC cables must be installed outdoors in adverse weather conditions, thus the cable material should be resistant to UV radiation, ozone, extreme temperature variations, and chemical erosion. Ordinary material cables used in this environment for an extended period of time will weaken the cable sheath and even dissolve the insulation layer. These conditions will not only immediately damage the cable system, but they will also raise the chance of short-circuiting the cable, as well as the likelihood of fires or worker injuries in the medium to long term, reducing the system's service life significantly.
Thus, the usage of PV-specific cables and components in PV power plants is critical. With the ongoing expansion of the solar industry, the market for photovoltaic supporting components has progressively arisen, and in terms of cables, a range of standards have been produced for photovoltaic specialised cable goods. Recently designed electron beam crosslinking cable, rated at 120 ℃, can survive tough climatic conditions and mechanical shock. Another example is the RADOX cable, which is a specialised solar energy cable designed in accordance with the international standard IEC216, with an outdoor service life that is 8 times that of rubber cables and 32 times that of PVC cables. Specialised photovoltaic cables and components offer superior weather resistance, UV and ozone erosion resistance, and can survive a wider range of temperature variations. In Europe, technicians discovered that the temperature levels measured on the roof can reach 100 to 110°C.
4. Cable Conductor Materials
DC cables are most commonly utilised in solar power stations for long-term outdoor operations; however, due to building limits, cable connections are primarily employed for connectors. Cable conductor materials are classified into copper core and aluminium core. Copper core cable has a better oxidation resistance than aluminium, long life, stability and performance to be good, small voltage drop and small power loss characteristics; in construction, due to the good flexibility of the copper core, the allowable bending radius is small, so easy to bend, easy to wear pipe; and the copper core fatigue, repeated bending is not easy to fracture, so easy to connect; at the same time, copper core mechanical strength is high, can On the contrary, aluminium core cable, due to its chemical qualities, is prone to oxidation (electrochemical reaction), and is especially prone to creep phenomena, which can lead to failure.
As a result, copper cables have significant benefits in solar power systems, particularly in the field of direct burial cable power delivery. It can reduce the number of accidents, enhance the dependability of the power supply, make construction and maintenance easier, and so on. This is precisely why copper cable is primarily used in underground cable power delivery in China.
5. Cable Insulation Sheath Materials
During the installation, operation, and maintenance of a photovoltaic power plant, the cable may be in the ground beneath the soil, overgrown rocks, the roof structure of the sharp edges of the wiring, or exposed in the air; the cable is likely to endure a variety of external impacts. If the cable jacket is insufficiently strong, the cable insulation will be damaged, thereby shortening the cable's life or causing short circuits, fires, and injury hazards. Cable researchers and technicians discovered that materials cross-linked with radiation have a higher mechanical strength than before the treatment. The crosslinking process alters the chemical structure of the polymer used in the cable insulation jacket material, converting the fusible thermoplastic material to a non-fusible elastomer material. Crosslinking radiation also significantly improves the thermal, mechanical, and chemical properties of the cable insulation.
DC circuits are frequently exposed to a range of unfavourable circumstances during operation, resulting in grounding and preventing the system from functioning properly. Extrusion, poor cable production, inadequate insulation materials, insufficient insulation performance, DC system insulation ageing, and the presence of specific damage faults can all induce grounding or become a grounding danger. Furthermore, the external climate, tiny animal invasion, or bite will all result in DC grounding issues. As a result, in this scenario, the cable sheath is generally armoured with a rodent-proof substance.