Improving module efficiency and expanding manufacturing capacity play complementary roles in reducing the cost of metal halide chalcogenide/silicon stacked solar modules. The U.S. Department of Energy's National Renewable Energy Laboratory (U.S. Department of Energy's National Renewable Energy Laboratory, NREL) researchers pointed out that: each cost leverage can play a similar role, depending on the manufacturer's ability to expand and improve the performance of the module.
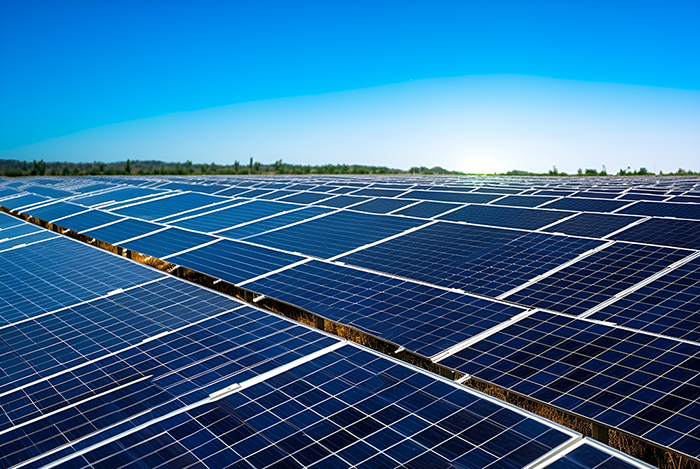
Most photovoltaic (PV) modules manufactured today are based on single-junction silicon solar cells, and by pairing silicon with another solar cell material (such as a metal halide) to form a stack of chalcogenides (MHPs), manufacturers can create solar modules. This can convert more sunlight into electricity than silicon alone.This stacking technology is still in its early stages, and there are a variety of options being sought to integrate MHPs, with many unknowns in terms of cost and performance. To address this gap, the researchers constructed a manufacturing cost model that will use existing devices and supply chain lab processes to compare different possible approaches at scale.
The researchers examined various approaches to building stacked modules and compared the sensitivity of manufacturing costs to the materials used to fabricate them, the number of device layers, the cost of producing the devices, the location of the factory, and other factors. They found that the factors that had the greatest impact on manufacturing costs were factory throughput and module efficiency.
"One of the questions this paper answers is: what is the value of this efficiency?" Jacob Cordell, lead author of the paper "Technoeconomic analysis of perovskite/silicon tandem solar modules," published in the journal Joule, said. "A key takeaway is that the 2.5% absolute efficiency gain in the modules provides the same cost reduction per unit of capacity as doubling the size of the plant."
Using the now publicly available Detailed Cost Analysis Model (DCAM), researchers were able to test a variety of scenarios, including locating plants in different parts of the world and different types of manufacturing incentives. By using the model, companies and researchers can use this baseline to examine how different processes and materials affect costs. The model does not address the energy productivity or lifetime of these modules, which are active areas of research.
Starting with a baseline model of a manufacturer making modules at 25 percent efficiency, with an annual production capacity of 3 gigawatts in the U.S., the researchers compared efficiency and manufacturing yields to determine how the cost of the modules varies as the amount of power generated increases. "This demonstrates the power of research in improving device efficiency and reducing the cost per watt of modules," Cordell said.
The journal article, authored by Michael Woodhouse and Emily Warren, notes that module efficiency is a dynamic variable in predicting the cost of stacked modules because many other variables have changed and will continue to change in order to be able to achieve the levels of efficiency and durability required for commercially viable PV. Stacked modules must be at least 25% efficient to be price competitive and used with other solar technologies. The next step in the commercialization of chalcogenide/silicon stacked modules is to improve the reliability of the technology and expand the area of efficient devices to full module size while maintaining performance.